Distaccanti per stampi | Lubrificanti industriali
Leader mondiali nell’innovazione per i distaccanti per stampi e lubrificanti industriali.
I distaccanti per stampi (lubrificanti industriali) sono parte integrante di numerosi processi produttivi. Speciali distaccanti per stampi possono contribuire ad accrescere la vostra produttività, prolungare la durata di attrezzi/stampi, aumentare i tempi di ciclo, migliorare la qualità di pezzi/superfici, oltre a ridurre il numero di scarti e di difetti, insieme a molti altri potenziali vantaggi garantiti dal prodotto.
Lavoriamo a stretto contatto con voi e i vostri team per trovare esattamente il distaccante per stampi adatto a migliorare i vostri processi.
Distaccanti per stampi convenzionali
Offriamo un ampio portfolio di distaccanti per stampi convenzionali (da applicare a ogni ciclo) per rispondere alle esigenze dei nostri clienti. I nostri distaccanti per stampi convenzionali sono:
- Disponibili a base acqua o a base solvente
- Disponibili nella versione pronta all’uso o da diluire, in base all’applicazione
- Idonei per molti tipi di teste ed ugelli di lubrifica
- Eventualmente disponibili con rapporti di diluizione “personalizzata”, a seconda dell’applicazione e dell’effetto distaccante necessario
- Eccellenti per pezzi stampati di forma complessa
- Prodotti con un livello eccezionalmente ridotto di residuo sugli stampi/incrostazione sugli stampi
Distaccanti per stampi semipermanenti
Potete ottenere una serie di potenziali vantaggi con le attuali tecnologie altamente sofisticate di distaccante per stampi a base di acqua o a base di solvente semipermanente. La tecnologia per il distacco semipermanente degli stampi ha fornito ai diversi settori una valida alternativa ai tradizionali distaccanti per stampi “spray da negozio” o da applicare a ogni ciclo e a volume elevato. I nostri clienti hanno riscontrato:
- Un numero maggiore di distacchi tra le applicazioni rispetto alle soluzioni di distaccanti convenzionali
- Più cicli di stampaggio possibili per turno di lavoro
- Quantità di prodotto minima per applicazione, per un ambiente di lavoro più pulito con inferiori esigenze di stoccaggio
- Riduzione globale degli scarti
- Gli stampi possono restare in funzione per periodi prolungati grazie alla protezione garantita
- Possibile la produzione di strutture complesse pezzi/stampo grazie alla facilità nell’ottenere applicazioni precise
- I pezzi stampati mantengono nel tempo l’estetica
Distaccanti per stampi senza silicone
Sempre all’avanguardia per innovazione e sostenibilità, Chem-Trend ha sviluppato una vasta gamma di distaccanti per stampi che non utilizzano silicone. I distaccanti per stampi senza silicone garantiscono una serie di vantaggi:
- Riducono i residui oleosi, permettendo operazioni più semplici di verniciatura e di rivestimento dopo il distacco
- Limitano il rischio di contaminazione e permettono di eliminare costose fasi dei processi produttivi
- Consentono di eliminare fasi del processo produttivo di numerosi componenti che risultano dispendiose in termini di costi e di tempistiche, di fatto accrescendo la produttività e tagliando i costi operativi
Perché dovreste scegliere i distaccanti per stampi Chem-Trend?
Autentico valore
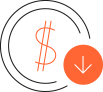
Creare valore per voi, il nostro cliente, è il nostro scopo principale. Formulata per ottimizzare le vostre operazioni quotidiane, la nostra linea di distaccanti per stampi, leader nel settore, si compone di prodotti a base di acqua e a base di solvente oltre a prodotti con e senza silicone in formulazioni semipermanenti oppure da applicare a ogni ciclo. Le nostre soluzioni possono aiutarti a superare costose sfide legate alla produzione, traendo vantaggio dalla forza dei distaccanti per stampi per migliorare l’efficienza operativa e la qualità del prodotto.
Produttività massimizzata
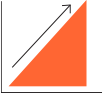
Chem-Trend permette di scegliere tra un’ampia gamma di distaccanti per stampi concepiti per rispondere alle esigenze individuali dei clienti e per ottimizzarne i risultati. Poiché ciascun processo di stampaggio è unico nel suo genere, per ottenere un distacco ottimale occorrono soluzioni specifiche. Il nostro team di esperti locali opera direttamente sul posto alla ricerca di tutti gli eventuali margini di miglioramento esistenti. Il nostro team di ricerca e sviluppo quindi progetta soluzioni personalizzate per le operazioni dei clienti.
Sostenibilità comprovata
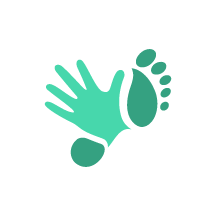
Molti dei nostri clienti lavorano diligentemente per rendere le loro operazioni più sostenibili. Scelgono Chem-Trend perché ci impegniamo a minimizzare l’impatto ambientale dei nostri prodotti da quando abbiamo iniziato la nostra attività. Abbiamo sviluppato il primo distaccante per stampi a base acqua negli anni ‘60, prodotto che ha avuto risvolti estremamente positivi per gli impianti di pressofusione in termini di salute e sicurezza, grazie all’abbandono dell’uso di grafite e/o solventi utilizzati nei lubrificanti per stampi in uso all’epoca. Il nostro costante impegno è focalizzato anche su altri fattori che incidono sull’impatto ambientale, quali l’uso dei COV nei distaccanti per stampi a base solvente. Oggigiorno, Chem-Trend è leader nel settore per lo sviluppo di soluzioni innovative.
Trova un distaccante per stampi con il nostro « Trova Soluzioni* » o contattaci oggi.
*Stai per lasciare questa pagina. Sarai reindirizzato al sito web Chem‑Trend globale dove troverai il contenuto richiesto in inglese.
NEWS
RIFLESSIONE CORRELATA
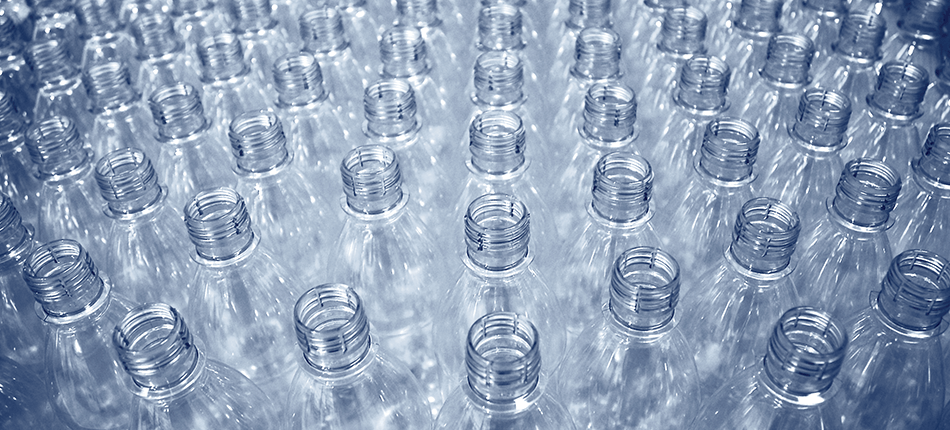
Ridurre al minimo i blocchi nelle linee di produzione di bottiglie in PET grazie al lubrificante Lusin® Lub O32F
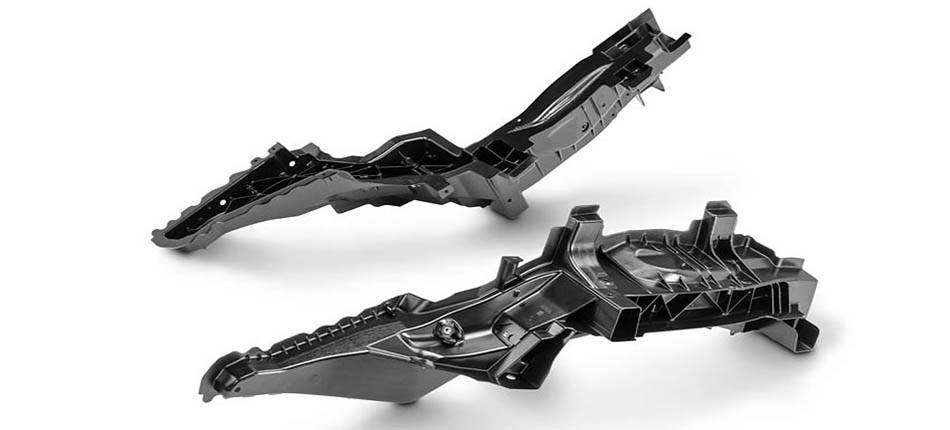
Il distaccante giusto per migliorare l’efficienza e la sostenibilità
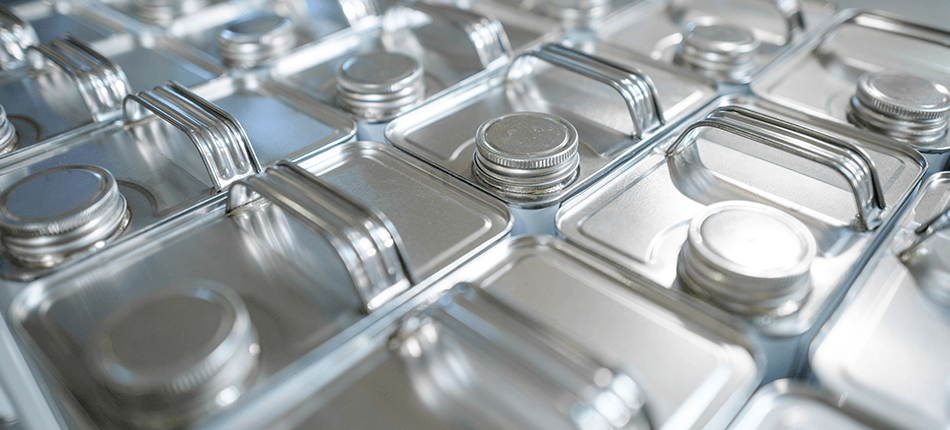
Distaccanti: L’adesione dei rivestimenti e l’utilizzo di prodotti complementari antistatici
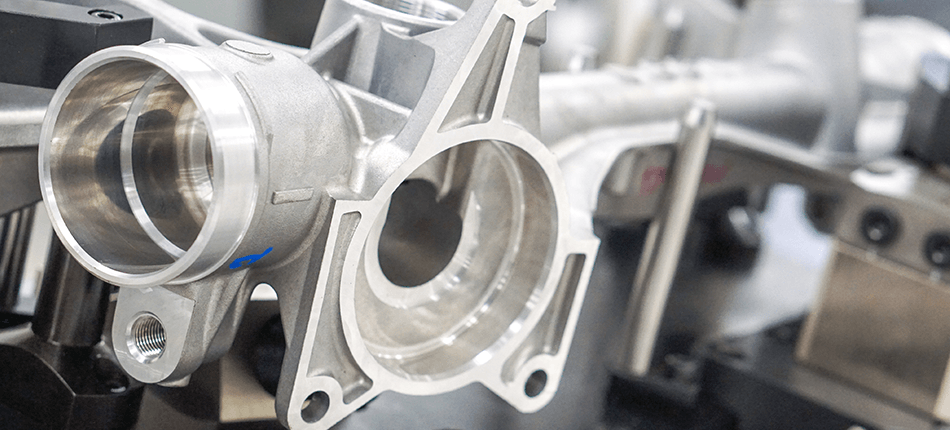
Gli effetti dei distaccanti sull’equilibrio termico degli stampi
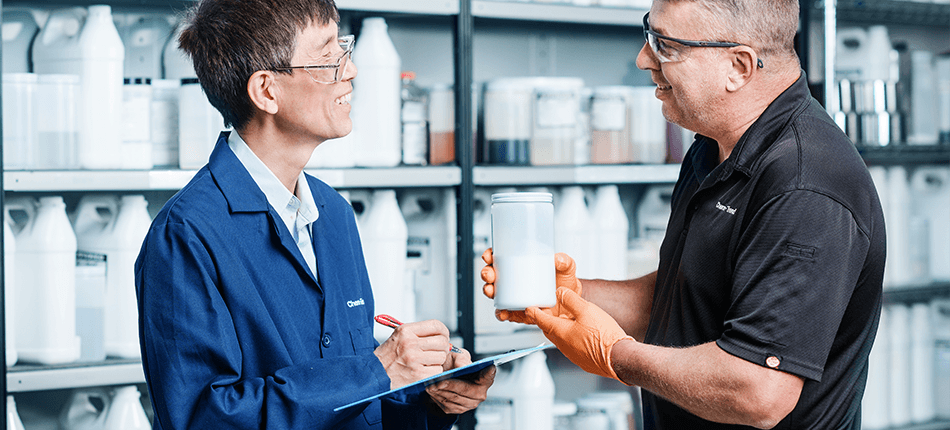
Tecnologie e tendenze nel settore dei distaccanti e dei lubrificanti per lo stampaggio dell’alluminio
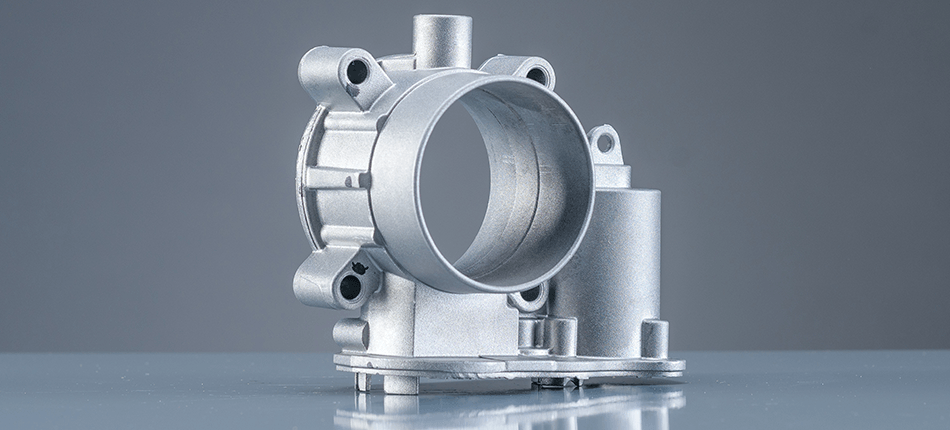
Tecnologie e tendenze nel settore dei distaccanti e dei lubrificanti per lo stampaggio di magnesio
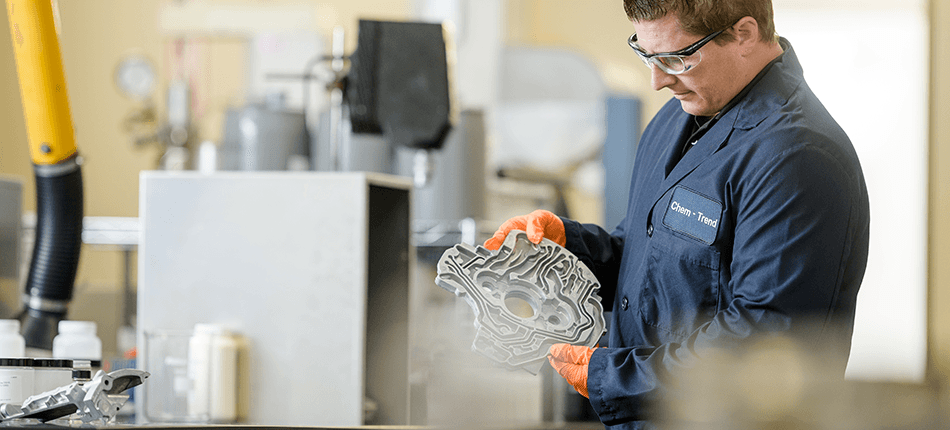
Tecnologie innovative per i distaccanti per stampi
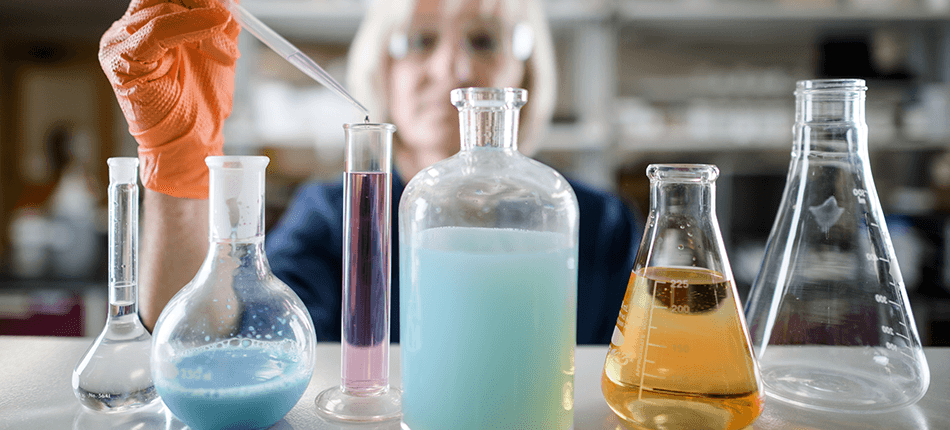
Tendenze innovative nel settore dei distaccanti per pressofusione per requisiti di produttività e di processo in evoluzione
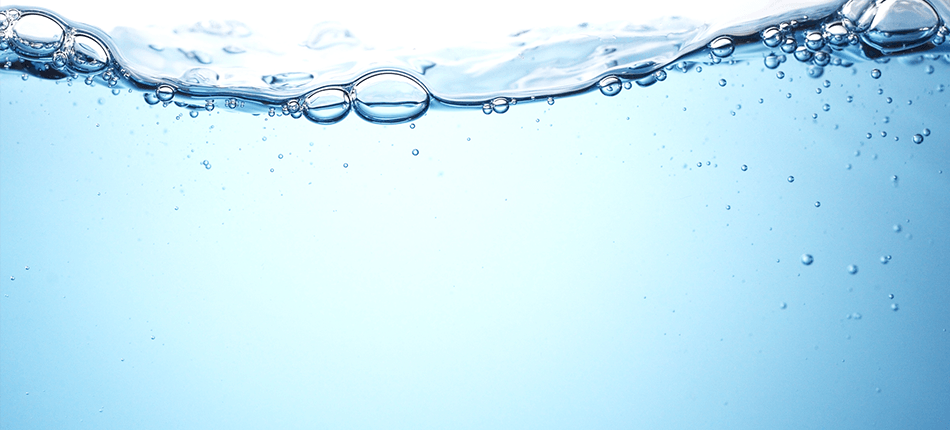
Tutela delle risorse idriche attraverso l’uso di distaccanti per pressofusione con prestazioni avanzate
BROCHURE
HERA™ – High Efficiency Release Agent – è un distaccante a base acqua, pronto all’uso e per applicazione Micro Spray.
Gli agenti distaccanti della serie HERA™ di Chem-Trend consentono di migliorare l’efficienza operativa attraverso varie modalità di riduzione degli scarti e della quantità di prodotto utilizzato.
I distaccanti HERA™-Light sono idonei per tutti i metodi di applicazione nella pressofusione
I distaccanti HERA™-Light garantiscono una buona adesione del film del distaccante in un ampio intervallo di temperature fornendo una sollecitazione termica minima per lo stampo, oltre ad una rapida formazione della pel film.
Scopri di più nel nostro dépliant.
I distaccanti Chem-Trend® SL-6XXXX supportano anche i processi dell’industria della rilavorazione
I componenti di colata prodotti usando i distaccanti Chem-Trend® SL-6XXXX sono CDC-compatibili e possono essere uniti mediante saldatura.
Scopri di più nel nostro dépliant.
Catalogo dei prodotti di manutenzione e dei distaccanti per stampi Lusin®
Soluzioni complete per una maggiore efficienza
Le nostre soluzioni per la manutenzione e il distacco degli stampi sono il migliore alleato dei vostri processi di produzione per aiutarvi ad aumentare l’efficienza e a ridurre i costi. Formando un sistema completo, i nostri prodotti per la manutenzione degli stampi Lusin® si integrano in maniera ideale, offrendovi numerosi vantaggi. Una regolare attività di manutenzione con i nostri detergenti e sgrassanti per stampi Lusin®, agenti protettivi e lubrificanti per stampi assicura la migliore cura possibile dei vostri stampi.
DOMANDE FREQUENTI
Il passaggio dipende in larga misura dai requisiti del settore e del processo. Diversi settori non tollerano più i prodotti a base di solventi per motivi di salute, sicurezza e ambiente o per altre questioni normative. Settori come la pressofusione, la produzione di pneumatici e lo stampaggio della gomma in generale utilizzano prevalentemente distaccanti a base acquosa. L’industria del poliuretano utilizza distaccanti per stampi sia a base di acqua che a base di solvente, mentre l’industria dei compositi e dei materiali termoplastici utilizza prevalentemente distaccanti a base di solvente.
I prodotti a base d’acqua sono più sensibili all’applicazione (e presentano maggiori difficoltà nella formazione della pellicola) e hanno tassi di evaporazione più lenti (che possono essere influenzati dal metodo di applicazione, dalle condizioni di processo e dai livelli di umidità dell’ambiente) rispetto ai prodotti a base di solvente.
I prodotti a base acquosa sono più inclini a causare interazioni chimiche tra l’acqua residua che rimane sulla superficie dello stampo e il materiale da stampare durante il processo di stampaggio (ad esempio, la generazione di sottoprodotti di urea nello stampaggio del poliuretano).
Questa categoria di distaccanti richiede inoltre una maggiore tecnologia per garantire la stabilità dell’emulsione e la resistenza alla bioattività. Queste sfide devono essere affrontate per espandere l’uso dei distaccanti a base di acqua in una gamma più ampia di settori.
I prodotti non aerosol si applicano al meglio nella lavorazione delle termoplastiche utilizzando una pistola a spruzzo di alta qualità o un’apparecchiatura di nebulizzazione con controllo orario.
La metodologia di applicazione dipende dal veicolo scelto, dalla natura del distaccante e dall’ambiente di processo. L’applicazione è un aspetto fondamentale da osservare e può influenzare in modo significativo le prestazioni del distaccante. Nella maggior parte dei casi, i distaccanti vengono applicati con una pistola a spruzzo (applicazione manuale o robotizzata). In alcune applicazioni si utilizzano sistemi di nebulizzazione programmabili con ugelli di nebulizzazione multipli che consentono l’applicazione di uno o più distaccanti. La dimensione dell’ugello viene regolata per garantire una corretta atomizzazione (influenzata dalla quantità prevista e dalla viscosità del distaccante) e una buona formazione di pellicola. L’applicazione a spruzzo può essere ad aria (in cui si utilizza l’aria per tagliare e atomizzare ulteriormente le gocce) o senza aria (in cui l’ugello, operando ad alta pressione, taglia il flusso del distaccante per ottenere la necessaria atomizzazione). Le pistole a spruzzo elettrostatiche possono essere utilizzate anche per applicare distaccanti solidi e liquidi. In alcune applicazioni, i distaccanti possono essere applicati anche tramite aerosol o persino mediante strofinamento manuale o automatizzato.
Ogni tipo di agente ha i suoi punti di forza (F) e i suoi limiti (L). Ecco una breve panoramica per tipo di distaccante:
Distaccanti a base di solvente:
F: più facili da applicare. Il veicolo solvente aiuta anche la formazione della pellicola. La velocità di evaporazione può essere regolata in base alla miscela di solventi. La scelta del solvente può facilitare la dissoluzione/dispersione dei principi attivi del distaccante.
L: Non altamente ecologici. Comportano maggiori problemi di salute (VOC) e di sicurezza (rischio di incendio) rispetto ai prodotti non a base di solventi.
Distaccanti a base d’acqua:
F: rispettano l’ambiente e non presentano rischi di incendio. A volte possono essere diluibili (possono essere spediti in come prodotti concentrati). Possono essere utilizzati per raffreddare lo stampo, se necessario. Possono essere sviluppati con un livello di tecnologia che garantisce prestazioni equivalenti a quelle dei distaccanti a base di solventi.
L: la loro produzione richiede una tecnologia più complessa. La corretta formazione della pellicola può essere più impegnativa. Questa categoria di distaccanti può essere maggiormente soggetta a problemi di stabilità e ad attacchi biologici. I distaccanti a base di acqua hanno tassi di evaporazione più lenti rispetto alle loro controparti a base di solvente e potrebbero non essere adatti per alcune operazioni di stampaggio a temperatura ambiente o con tempi di ciclo brevi. L’acqua residua sullo stampo può influire sulle prestazioni di stampaggio (vapore intrappolato) o addirittura reagire chimicamente con il materiale da stampare. Quest’ultimo aspetto è particolarmente problematico quando si stampano parti in poliuretano.
Distaccanti senza veicolo:
F: possono essere applicati “così come sono” grazie all’assenza di veicolo. Nessuna emissione di vapori. Si osserva un’applicazione meno rumorosa. Non richiedono diluizione o stoccaggio in serbatoi. Nessun flusso di rifiuti.
L: possono creare un pericolo di polvere se non applicati correttamente. Necessitano di attrezzature speciali per l’applicazione (spesso pistole a spruzzo elettrostatiche), che possono richiedere costosi investimenti. L’uso di distaccanti senza veicolo: può anche richiedere ulteriori modifiche all’attrezzatura di stampaggio per garantire il bilanciamento termico dello stampo. Questi fattori spesso limitano l’applicazione di questa categoria di distaccanti.
Distaccanti sacrificali:
F: facili da applicare. Richiedono minore tecnica di applicazione e offrono una maggiore tolleranza di lavoro (dipendono meno da operatori formati).
L: tendono ad accumularsi sullo stampo se applicati in quantità o in modo eccessivo. In generale, il rivestimento distaccante viene parzialmente trasferito al pezzo stampato, con conseguenti potenziali effetti collaterali negativi sulle operazioni post-stampaggio (verniciatura, adesione, ecc.) se applicato in eccesso o se la chimica del distaccante non è compatibile con l’operazione post-stampaggio. Se a base d’acqua, tendono a raffreddare lo stampo, rimuovendo calore ed energia dal sistema (ciò può rappresentare uno svantaggio se il processo non è stato progettato a tale scopo).
Distaccanti semi-permanenti:
F: richiedono una frequenza di applicazione significativamente inferiore rispetto ai distaccanti sacrificali, poiché la pellicola di distaccante dura per più cicli di stampaggio (la frequenza dipende dalle condizioni del processo). Consentono una produzione più costante e continua senza interruzioni per l’applicazione del distaccante. Il trasferimento al pezzo stampato è minimo, il che consente di migliorare le operazioni successive allo stampaggio (rivestimento, adesione). Il distaccante può essere riapplicato regolarmente sullo stampo rivestito, rinfrescando la pellicola di distaccante. Questa categoria di distaccanti offre un’eccellente combinazione di barriere chimiche e fisiche, impedendo l’accumulo e fornendo le prestazioni di distacco desiderate.
L: richiedono una maggiore formazione degli operatori per garantire la giusta frequenza di ritocco. Gli stampi devono essere puliti per consentire una buona interazione tra il distaccante e la superficie dello stampo durante l’applicazione iniziale del distaccante.
Distaccanti interni:
F: riducono la necessità di distaccanti esterni.
L: possono continuare a trasudare sulla superficie nel tempo, compromettendo le operazioni successive allo stampaggio (rivestimento e adesione) o l’aspetto superficiale del pezzo. Spesso non eliminano la necessità di utilizzare distaccanti esterni, poiché i distaccanti interni allo stampo non sempre migrano verso l’interfaccia dello stampo o possono non garantire un’efficienza di distacco del 100%. Limitati nella loro capacità di svolgere le funzioni di distaccante ad alte prestazioni come influire sulle caratteristiche superficiali del pezzo.
Il vantaggio dei distaccanti contenenti silicone è che offrono un ottimo effetto distaccante. Lo svantaggio dei distaccanti contenenti silicone è che il trattamento successivo dei pezzi sformati, come l’incollaggio o la verniciatura, può essere difficile o addirittura impossibile. Sarà necessario un ulteriore trattamento dei pezzi dopo lo stampaggio.
I distaccanti per stampi non solo forniscono una barriera fisica e/o chimica come mezzo di separazione tra il materiale da stampare e la superficie dello stampo, ma hanno anche un impatto sulle caratteristiche del processo, come la portata del materiale da stampare all’interno della cavità dello stampo, il tempo del ciclo di stampaggio e, naturalmente, la facilità di distacco. La scelta dei distaccanti per stampi influisce anche sulle caratteristiche di finitura del pezzo sformato, come il livello di lucentezza, l’accurata riproduzione della texture, le operazioni successive allo stampaggio (ad esempio, l’adesione o il rivestimento del pezzo stampato), oltre a influenzare la durata dello stampo tra i cicli di manutenzione e la produttività complessiva.
I fattori da considerare per la scelta del distaccante adeguato includono:
- Materiale dello stampo / substrato
- Materiale da stampare
- Condizioni di processo:
– Temperatura
– Velocità della linea/tempo di ciclo
– Pressione
– Processo di stampaggio specifico, come stampaggio a iniezione, alta pressione, riempimento per gravità, compressione, ecc.
– Fluttuazioni delle variabili di processo - Geometria dello stampo
- Operazioni post-stampaggio (adesione, rivestimento)
- Livello di prestazione e produttività previsti (numero di rilasci buoni o pezzi buoni sformati per periodo di tempo)
- Problemi di processo esistenti (difficoltà di riempimento della cavità, saldatura, tassi di scarto legati al distacco, fluttuazioni delle condizioni di processo, ecc.)
- Aspettative di manutenzione dello stampo (frequenza di pulizia dello stampo)
- Requisiti di finitura dei pezzi (lucentezza, marezzatura, ecc.)
- Metodologia di applicazione
- Requisiti di salute, sicurezza e ambiente (HSE)
L’applicazione di una quantità eccessiva di distaccante può rendere più difficoltoso il successivo trattamento di processo dei pezzi, creando una superficie oleosa o scivolosa sul pezzo stampato.
Il vantaggio delle bombolette aerosol per la lavorazione di materiali termoplastici è che il sistema di valvole di nebulizzazione consente di applicare il prodotto in uno strato molto sottile, in modo costante e con uno schema di spruzzo prevedibile. Ciò consente di risparmiare materiale e di evitare un’applicazione eccessiva. Le bombolette spray offrono inoltre facilità di manipolazione e flessibilità.
L’accumulo di distaccanti, di materiale da stampare o sottoprodotti e di residui generati dalle reazioni chimiche che avvengono all’interno della cavità dello stampo (in situazioni in cui il composto viene modificato chimicamente durante il processo di stampaggio) influisce negativamente sulle prestazioni dello stampaggio in termini di trasferimento del calore, proprietà dimensionali del pezzo, aspetto estetico ed efficienza del processo.
Le incrostazioni della cavità dello stampo devono essere regolarmente rimosse meccanicamente o chimicamente per garantire la qualità del pezzo. Ogni volta che lo stampo deve essere pulito in loco o altrimenti sottoposto a manutenzione, si perde produttività.
I problemi di accumulo possono essere causati da due fonti principali:
Eccesso di distaccante presente sullo stampo.
Questo può essere il risultato di una scelta inadeguata del distaccante per l’applicazione specifica (ad esempio, non compatibile con la temperatura di processo) o di un’applicazione eccessiva di distaccante sullo stampo.
Mancanza di barriera per il distacco che causa l’accumulo del materiale da stampare o di sottoprodotti e residui generati durante il processo di stampaggio
In questo caso, la scelta del distaccante potrebbe non essere adeguata alle condizioni del processo (non adatto alla temperatura del processo, scarsa formazione di pellicola, ecc.) Ciò può essere causato anche da carenze nell’applicazione (non sufficiente pellicola di distaccante presente sullo stampo) o dalla mancanza di resistenza fisica e/o chimica del distaccante al materiale che quindi penetra nella pellicola di distaccante e aderisce fisicamente o chimicamente allo stampo.
Le industrie stampano sempre più materiali esotici per produrre pezzi con prestazioni migliori in condizioni sempre più difficili in cui operano i prodotti finiti. Questi materiali esotici non sono sempre facili da stampare. Un valido esempio viene dal settore automobilistico, dove i componenti del motore (parti stampate) sono soggetti a sfide chimiche e fisiche per resistere a condizioni operative più aggressive. Di conseguenza, i materiali di nuova concezione e più resistenti devono essere stampati ad alti ritmi di produzione con livelli di scarto minimi. Ciò rappresenta una sfida per l’industria dei distaccanti, a causa delle loro proprietà chimiche e fisiche che ne rendono difficile lo stampaggio e il distacco.
Anche l’aspetto dei pezzi è diventato più esigente e in molti casi i pezzi vengono utilizzati così come stampati, con una finitura successiva minima. L’industria automobilistica richiede che i componenti altamente visibili, come i volanti o i cruscotti, presentino proprietà estetiche molto rigorose (ad esempio, texture, lucentezza e resistenza alle abrasioni) subito dopo la sformatura.
Negli ultimi anni la pressofusione di alluminio ad alta pressione ha visto un aumento della complessità degli stampi, con un incremento della colata ad alta integrità (semisolida e a spremitura), nonché una riduzione dei tempi di ciclo e un ulteriore aumento delle temperature degli stampi.
Questi fattori richiedono che il distaccante fornisca migliori proprietà anti-saldatura e migliori proprietà di distacco e lubrificazione per produrre pezzi di qualità in condizioni di colata più difficili. Questo obiettivo deve essere raggiunto senza compromettere altre caratteristiche prestazionali del distaccante.
Progetti di stampi più complessi e sofisticati vengono creati anche per altri settori, come quello degli pneumatici a basso profilo realizzati dai produttori di pneumatici. Questi progetti di stampi pongono ai distaccanti requisiti più elevati in termini di facilità di distacco e flusso di gomma. Anche l’aspetto post-stampaggio degli pneumatici è di importanza critica e comporta sfide significative per sformare facilmente questi tipi di pneumatici e allo stesso tempo raggiungere standard estetici elevati.
L’uso di prodotti a basso contenuto di VOC (composti organici volatili) continua a essere imposto dagli impianti di produzione a seguito delle normative HSE, ed è particolarmente importante nei processi che richiedono un maggiore coinvolgimento diretto degli operatori, come nel segmento dei compositi. L’attenzione per lo sviluppo di prodotti più rispettosi dell’ambiente e più sicuri da usare continuerà ad aumentare. Ciò stimolerà lo sviluppo di nuovi distaccanti per soddisfare queste esigenze, pur garantendo lo stesso livello di prestazioni, o un livello superiore, dei prodotti attualmente in uso.
I distaccanti consegnati alla rinfusa possono essere applicati al meglio per mezzo di una pistola a spruzzo o di un nebulizzatore a ciclo controllato.
I prodotti non aerosol si applicano al meglio utilizzando una pistola a spruzzo di alta qualità o un’apparecchiatura di nebulizzazione con controllo orario.